With the continuous improvement of human requirements for the living environment, the environmental problems involved in the current PCB production process are particularly prominent. The topic of lead and bromine is currently the hottest topic; lead-free and halogen-free will affect PCB development in many ways. Although the changes in the surface finish process of PCBs are not very big at present, it seems to be a relatively distant thing, but it should be noted that long-term slow changes will lead to huge changes. Under the circumstance that the voice of environmental protection is getting higher and higher, the surface finish of PCB will definitely undergo great changes in the future.
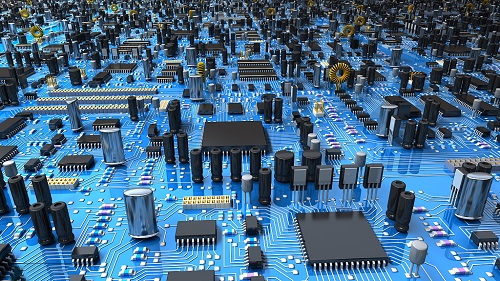
Purpose of surface finish
The most basic purpose of surface finish is to ensure good solder ability or electrical properties. Since copper in nature tends to exist in the form of oxides in the air and is unlikely to remain as raw copper for long periods of time, additional treatment of the copper is required. Although strong flux can be used to remove most copper oxides in subsequent assembly, strong flux itself is not easy to remove, so the industry generally does not use strong flux.
Common five surface finish technology
- Hot air leveling (spray tin)
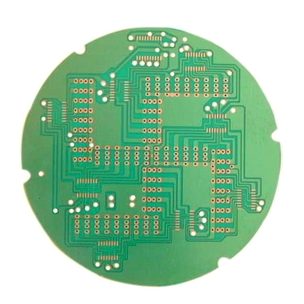
Hot air leveling, also known as hot air solder leveling, is a process of coating molten tin-lead solder on the surface of the PCB and flattening (blowing) it with heated compressed air to form a layer that resists copper oxidation and provides good solderability. Sexual coating. Solder and copper form copper-tin intermetallics at the junction during hot air leveling. The thickness of the solder to protect the copper surface is about 1-2 mils. PCBs are hot air leveled by immersion in molten solder; air knives blow liquid solder before it solidifies; air knives minimize solder meniscus on copper surfaces and prevent solder bridging. Hot air leveling is divided into two types: vertical type and horizontal type. It is generally considered that the horizontal type is better, mainly because the horizontal type hot air leveling is more uniform and can realize automatic production. The general process of the hot air leveling process is: micro-etching → preheating → flux coating → tin spraying → cleaning.
- Organic coating (OSP)
The organic coating process is different from other surface finish processes in that it acts as a barrier between copper and air; the simplicity and low cost of the organic coating process make it widely used in the industry. The early organic coating molecules are imidazoles and benzotriazoles that play a role in rust prevention, and the latest molecules are mainly benzimidazoles, which are chemically bonded nitrogen functional groups to copper on the PCB. In the subsequent soldering process, if only one organic coating layer on the copper surface is not acceptable, there must be many layers. This is why copper baths are usually added to chemical tanks. After coating the first layer, the coating layer adsorbs copper; then the organic coating molecules of the second layer combine with copper until twenty or even hundreds of times the organic coating molecules are assembled on the copper surface, which can ensure multiple cycles. flow soldering. Tests have shown that the latest organic coating process maintains good performance over multiple lead-free soldering processes. The general flow of the organic coating process is: degreasing→micro-etching→pickling→pure water cleaning→organic coating→cleaning, and the process control is easier than other surface finish processes.
- Electroless Nickel/Immersion Gold (Immersion Gold)
The electroless nickel/immersion gold process is not as simple as organic coating, and the electroless nickel/immersion gold seems to put a thick armor on the PCB; in addition, the electroless nickel/immersion gold process is not like an organic coating as a rust barrier. , it can be useful in the long-term use of the PCB and achieve good electrical performance. Therefore, electroless nickel plating/immersion gold is to wrap a thick layer of nickel-gold alloy with good electrical properties on the copper surface, which can protect the PCB for a long time; in addition, it also has environmental tolerance that other surface treatment processes do not have. sex. The reason for nickel plating is that gold and copper interdiffusion, and the nickel layer prevents the diffusion of gold and copper; without the nickel layer, the gold would diffuse into the copper within hours. Another benefit of electroless nickel/immersion gold is the strength of nickel, as only 5 microns of nickel can limit Z-direction expansion at high temperatures. In addition, electroless nickel/immersion gold also prevents the dissolution of copper, which will benefit lead-free assembly. The general process of electroless nickel plating / immersion gold process is: acid cleaning → micro-etching → pre-dipping → activation → electroless nickel plating → chemical immersion gold, there are mainly 6 chemical tanks, involving nearly 100 kinds of chemicals, so the process control comparison difficulty.
- Immersion Silver
The immersion silver process is between organic coating and electroless nickel/immersion gold. The process is relatively simple and fast; it is not as complicated as electroless nickel/immersion gold, nor does it put a thick layer of armor on the PCB, but it Still able to provide good electrical performance. Silver is gold’s little brother and retains good solderability even when exposed to heat, humidity and pollution, but loses its luster. Immersion silver does not have the good physical strength of electroless nickel/immersion gold because there is no nickel under the silver layer. Immersion silver is a displacement reaction, which is almost a submicron coating of pure silver. Sometimes the immersion silver process also contains some organic matter, mainly to prevent silver corrosion and eliminate silver migration problems; it is generally difficult to measure this thin layer of organic matter, and analysis shows that the weight of the organic matter is less than 1%.
5.Immersion tin
Since all current solders are based on tin, the tin layer can be matched to any type of solder. From this point of view, the immersion tin process has great prospects for development. However, tin whiskers appeared in the previous PCB after the tin immersion process, and the migration of tin whiskers and tin during the soldering process would bring reliability problems, so the adoption of the tin immersion process was limited. Later, organic additives were added to the tin immersion solution, which made the tin layer structure have a granular structure, which overcomes the previous problems, and also has good thermal stability and solderability. The immersion tin process can form a flat copper-tin intermetallic compound, which makes immersion tin have the same good solderability as hot air leveling without the headache of hot air leveling; immersion tin also does not have electroless nickel plating / Diffusion problem between immersion gold metals – copper-tin intermetallic compounds can be firmly bonded together. The tin immersion board cannot be stored for too long, and the assembly must be carried out according to the order of tin immersion.
6.Other surface Finish processes
There are few applications of other surface finish processes. Let’s take a look at the relatively more nickel-gold electroplating and electroless palladium plating processes. Electroplating Nickel-gold is the originator of PCB surface treatment technology. It has appeared since the appearance of PCB, and has gradually evolved into other methods. It is to first coat a layer of nickel and then a layer of gold on the surface conductor of the PCB. Nickel plating is mainly to prevent the diffusion between gold and copper. There are two types of electroplated nickel gold: soft gold plating (pure gold, the gold surface does not look bright) and hard gold plating (the surface is smooth and hard, wear-resistant, contains other elements such as cobalt, and the gold surface looks brighter). Soft gold is mainly used for gold wire in chip packaging; hard gold is mainly used for electrical interconnection in non-soldering places. Considering the cost, the industry often uses image transfer to reduce the use of gold by selective electroplating. At present, the use of selective gold plating in the industry continues to increase, mainly due to the difficulty in controlling the electroless nickel plating/immersion gold process. Under normal circumstances, welding will cause electroplated gold to become brittle, which will shorten the service life, so avoid welding on electroplated gold; but electroless nickel plating/immersion gold is very thin and consistent, and embrittlement rarely occurs. . The process of electroless palladium plating is similar to that of electroless nickel plating. The main process is to reduce palladium ions to palladium on the catalytic surface by a reducing agent (such as sodium dihydrogen hypophosphite). The advantages of electroless palladium plating are good soldering reliability, thermal stability, and surface flatness.
Selection of Surface finish Process
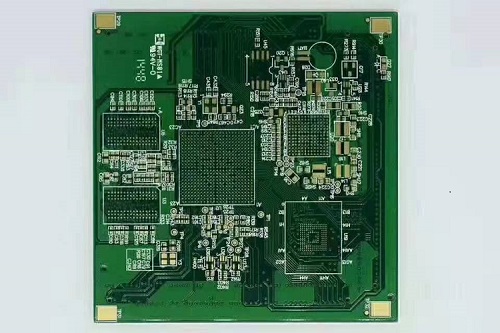
The choice of surface finish process mainly depends on the type of final assembly components; the surface finish process will affect the production, assembly and final use of the PCB. The following will specifically introduce the use of five common surface finish processes.
- Hot air leveling (spray tin)
Hot air leveling once dominated the PCB surface finish process. In the 1980s, more than three-quarters of PCBs used hot air leveling, but the industry has been reducing the use of hot air leveling over the past decade, and it is estimated that about 25%-40% of PCBs are currently used. Hot air leveling process. The dirty, smelly, and dangerous process of hot air leveling has never been a favorite process, but it is an excellent process for larger components and larger pitch wires. In a PCB with a higher density, the flatness of the hot air leveling will affect the subsequent assembly; therefore, the HDI board generally does not use the hot air leveling process. With the advancement of technology, the industry has now developed a hot air leveling process suitable for QFP and BGA with smaller assembly pitch, but there are few practical applications. At present, some factories use organic coating and electroless nickel plating/immersion gold process to replace hot air leveling process; technological development also makes some factories use immersion tin and immersion silver process. Coupled with the trend of lead-free in recent years, the use of hot air leveling is further restricted. Although so-called lead-free hot air leveling has appeared, this may involve equipment compatibility issues.
- Organic Coating (OSP)
It is estimated that about 25%-30% of PCBs currently use an organic coating process, and the proportion has been rising . The organic coating process can be used on low-tech PCBs or high-tech PCBs, such as single-sided TV PCBs and high-density chip packaging boards. For BGA, organic coating applications are also more. If the PCB does not have surface connection functional requirements or shelf life limitations, organic coating will be the most ideal surface finish process.
- Electroless nickel plating/immersion gold (chemical immersion gold)
The electroless nickel plating/immersion gold process is different from organic coating. It is mainly used on boards with surface connection functional requirements and long storage periods, such as mobile phone keypads , the edge connection area of the router casing and the electrical contact area for elastic connection of the chip processor. Electroless nickel/immersion gold was widely used in the 1990s due to the flatness problem of hot air leveling and the removal of organically coated flux; The application of immersion gold / immersion gold process has decreased, but almost every high-tech PCB factory has electroless nickel / immersion gold wire. Considering the brittleness of the solder joints when removing Cu-Sn intermetallics, there are many problems with the relatively brittle Ni-Sn intermetallics. Therefore, almost all portable electronic products (such as mobile phones) use copper-tin intermetallic compound solder joints formed by organic coating, immersion silver or immersion tin, and use electroless nickel plating/immersion gold to form key areas, contact areas and EMI shielding areas . It is estimated that about 10%-20% of PCBs currently use electroless nickel/immersion gold processes.
- Immersion silver
Immersion silver is cheaper than electroless nickel plating/immersion gold. If the PCB has connection functional requirements and needs to reduce costs, immersion silver is a good choice; plus the good flatness and contact of immersion silver , then you should choose the immersion silver process. There are many applications of immersion silver in communication products, automobiles, and computer peripherals, and immersion silver is also used in high-speed signal design. Because immersion silver has good electrical properties unmatched by other surface treatments, it can also be used in high frequency signals. EMS recommends the immersion silver process because of its ease of assembly and better inspectability. However, the growth of immersion silver is slow (but not declining) due to shortcomings such as tarnishing and solder joint voids. It is estimated that about 10%-15% of PCBs currently use the immersion silver process.
- Immersion tin
Tin has been introduced into the surface finish process for nearly ten years, and the emergence of this process is the result of the requirements of production automation. Immersion tin does not introduce any new elements in the soldering place, especially suitable for communication backplanes. Tin will lose solderability beyond the shelf life of the board, so immersion tin requires better storage conditions. In addition, the use of tin immersion process is restricted due to the presence of carcinogens. It is estimated that about 5%-10% of PCBs currently use the immersion tin process.
As customer requirements are getting higher and higher, environmental requirements are getting stricter, and surface finish processes are becoming more and more numerous, it seems a bit dazzling and confusing to choose the kind of surface treatment process that has development prospects and greater versatility. . Where the PCB surface treatment process will go in the future cannot be accurately predicted now. In any case, meeting customer requirements and protecting the environment must come first!
If you have any PCB demands, please feel free to contact us.
Email:[email protected]
Skype:[email protected]
Telephone number:+86 133 9241 2348
Whatsapp: +86 133 9241 2348