In general, the stack-up design mainly follows two rules:
- Each trace layer must have an adjacent reference layer (power or ground);
- The adjacent main power supply layer and ground layer should maintain a minimum distance to provide larger coupling capacitance;
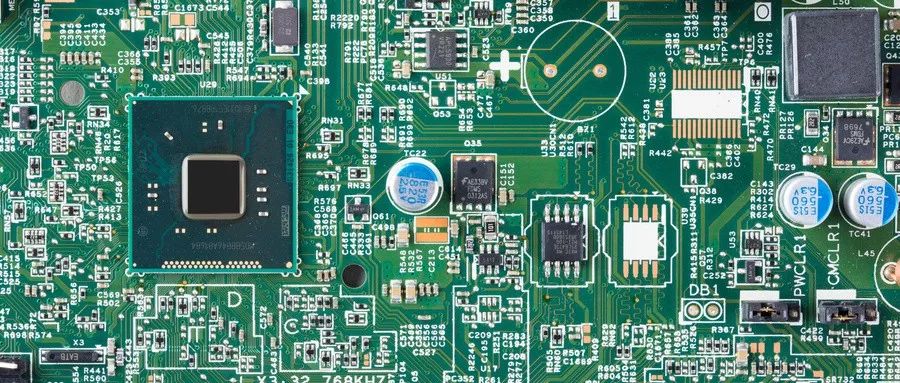
The stackup from two-layer board to eight-layer board is listed below for example:
- Lamination of single-sided PCB board and double-sided PCB board
For two-layer boards, there is no stacking problem due to the small number of layers. Controlling EMI radiation is mainly considered from wiring and layout;
The electromagnetic compatibility problem of single-layer board and double-layer board is becoming more and more prominent. The main reason for this phenomenon is that the signal loop area is too large, which not only produces strong electromagnetic radiation, but also makes the circuit sensitive to external interference. The easiest way to improve the electromagnetic compatibility of a circuit is to reduce the loop area of critical signals.
Key signals: From the perspective of electromagnetic compatibility, key signals mainly refer to signals that generate strong radiation and signals that are sensitive to the outside world. Signals that can generate strong radiation are generally periodic signals, such as low-order signals of a clock or an address. Signals that are sensitive to interference are those analog signals with lower levels.
Single and double layer boards are usually used in low frequency analog designs below 10KHz:
1) The power traces on the same layer are routed radially, and the sum of the lengths of the wires is minimized;
2) When running the power and ground wires, they should be close to each other; lay a ground wire on the side of the key signal wire, and this ground wire should be as close to the signal wire as possible. In this way, a smaller loop area is formed and the sensitivity of differential mode radiation to external interference is reduced. When a ground wire is added next to the signal wire, a loop with the smallest area is formed, and the signal current will definitely take this loop instead of other ground paths.
3) If it is a double-layer circuit board, you can lay a ground wire along the signal line on the other side of the circuit board, close to the signal line, and the line should be as wide as possible. The loop area thus formed is equal to the thickness of the circuit board multiplied by the length of the signal line.
- Lamination of four-layer boards
- SIG-GND(PWR)-PWR (GND)-SIG;
- GND-SIG(PWR)-SIG(PWR)-GND;
For the above two stack-up designs, the potential problem is for the traditional 1.6mm (62mil) board thickness. The layer spacing will become very large, which is not only unfavorable for controlling impedance, interlayer coupling and shielding; especially, the large spacing between the power supply ground layers reduces the board capacitance and is not conducive to filtering noise.
For the first solution, it is usually applied to the situation where there are many chips on the board. This solution can get better SI performance, but it is not very good for EMI performance, which is mainly controlled by wiring and other details. Main attention: The formation is placed on the connecting layer of the signal layer with the most dense signal, which is conducive to absorbing and suppressing radiation; increasing the board area to reflect the 20H rule.
For the second solution, it is usually used when the chip density on the board is low enough and there is enough area around the chip (where the required power supply copper layer is placed). In this scheme, the outer layers of the PCB are the ground layers, and the two middle layers are the signal/power layers. The power supply on the signal layer is routed with a wide wire, which can make the path impedance of the power supply current low, and the impedance of the signal microstrip path is also low, and can also shield the inner layer signal radiation through the outer ground. From an EMI control standpoint, this is the best 4-layer PCB structure available.
Main attention: the distance between the two middle layers of signal and power mixed layers should be widened, and the wiring direction should be vertical to avoid crosstalk; the board area should be properly controlled to reflect the 20H rule; if the wiring impedance is to be controlled, the above scheme should be very careful. Arranged under the power and ground copper islands. In addition, the copper layers on the power or ground planes should be interconnected as much as possible to ensure DC and low frequency connectivity.
3.Three or six-layer laminates
For the design with high chip density and high clock frequency, the design of 6-layer board should be considered. The recommended stacking method is:
1.SIG-GND-SIG-PWR-GND-SIG;
For this scheme, this stack-up scheme can achieve better signal integrity, the signal layer is adjacent to the ground layer, the power layer and the ground layer are paired, the impedance of each trace layer can be well controlled, and the two The formation is able to absorb the magnetic field lines well. And in the case of complete power supply and ground layer, it can provide a better return path for each signal layer.
- GND-SIG-GND-PWR-SIG-GND;
For this kind of scheme, this kind of scheme is only suitable for the case where the device density is not very high, this kind of stack has all the advantages of the above stack, and the ground plane of the top and bottom layers is relatively complete, which can be used as a better shielding layer to use. It should be noted that the power layer should be close to the layer that is not the main component side, because the bottom plane will be more complete. Therefore, the EMI performance is better than the first solution.
Summary: For the scheme of the six-layer board, the distance between the power layer and the ground layer should be minimized to obtain good power and ground coupling. However, with a thickness of 62 mil, although the layer spacing has been reduced, it is not easy to control the distance between the main power supply and the ground layer to be very small. Comparing the first scheme with the second scheme, the cost of the second scheme is greatly increased. Therefore, we usually choose the first solution when stacking. When designing, follow the 20H rule and mirror layer rule design.
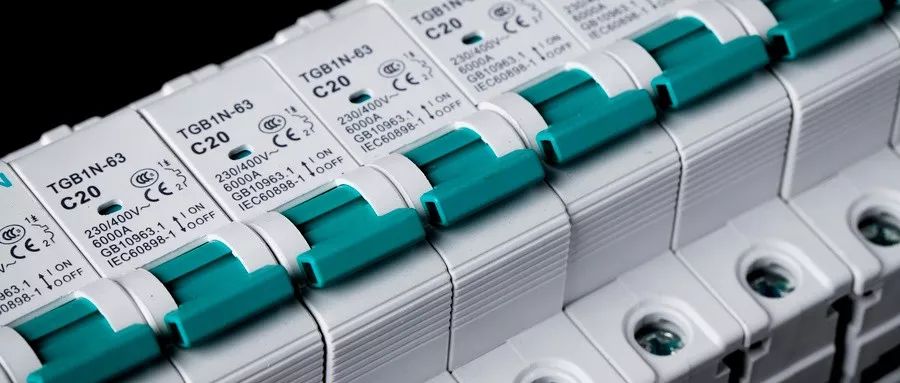
4.Lamination of four and eight-layer boards
- This is not a good stacking method due to poor electromagnetic absorption capacity and large power supply impedance. Its structure is as follows:
- Signal 1 component surface, microstrip trace layer
- Signal 2 internal microstrip routing layer, better routing layer (X direction)
- Ground
- Signal 3 strip line routing layer, better routing layer (Y direction)
- Signal 4 stripline routing layer
- Power
- Signal 5 internal microstrip routing layer
- Signal 6 microstrip trace layer
- It is a variant of the third stacking method. Due to the addition of the reference layer, it has better EMI performance, and the characteristic impedance of each signal layer can be well controlled.
- Signal 1 component surface, microstrip wiring layer, good wiring layer
- Ground formation, better electromagnetic wave absorption ability
- Signal 2 strip line routing layer, good routing layer
- Power supply layer, with the underlying formation constitutes excellent electromagnetic absorption 5.Ground formation
- Signal 3 strip line routing layer, good routing layer
- Power ground, with larger power impedance
- Signal 4 microstrip routing layer, good routing layer
- The best stacking method, due to the use of multi-layer ground reference planes, has very good geomagnetic absorption capacity.
- Signal 1 component surface, microstrip wiring layer, good wiring layer
- Ground formation, better electromagnetic wave absorption ability
- Signal 2 strip line routing layer, good routing layer
- Power supply layer, with the underlying formation constitutes excellent electromagnetic absorption 5.Ground formation
- Signal 3 strip line routing layer, good routing layer
- Ground formation, better electromagnetic wave absorption ability
- Signal 4 microstrip routing layer, good routing layer
How to choose how many layers of boards to use and how to stack them depends on many factors such as the number of signal networks on the board, device density, PIN density, signal frequency, and board size. We have to take these factors into consideration. The more the number of signal networks, the greater the device density, the greater the PIN density, and the higher the frequency of the signal, the multi-layer board design should be used as much as possible. For good EMI performance it is best to ensure that each signal layer has its own reference layer.
If you have any PCB demands, please feel free to contact us.
Email:[email protected]
Skype:[email protected]
Telephone number:+86 133 9241 2348
Whatsapp: +86 133 9241 2348