HDI board introduction
HDI board, that is, high-density interconnection board, is a circuit board with relatively high line distribution density using micro-blind buried via technology. The HDI board has inner and outer circuits. Drilling and metallization in the holes are used to connect the inner circuits of each layer.
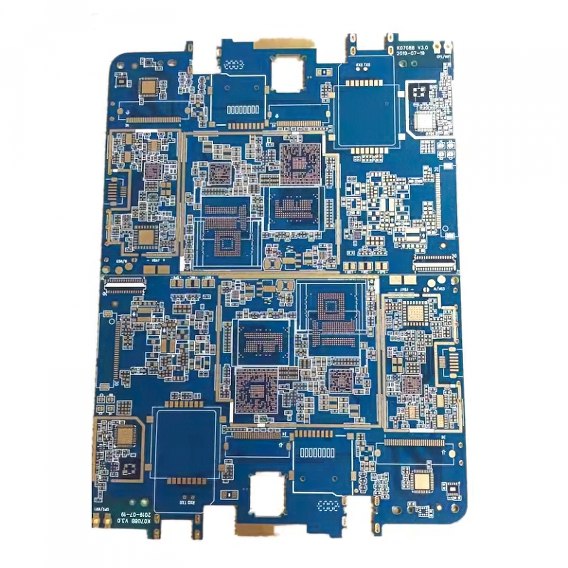
HDI boards are generally manufactured by layer-by-layer method, the more the number of layers, the higher the technical grade of the plate. Ordinary HDI boards are basically one-time build-up. High-end HDI uses two-time or more build-up technology. At the same time, advanced PCB technologies such as stacking holes, electroplating and filling holes, and laser direct drilling are used.
When the density of the PCB increases beyond the eight-layer board, it is manufactured with HDI, and its cost will be lower than that of the traditional complex pressing process. HDI board is conducive to the use of advanced packaging technology, and its electrical performance and signal accuracy are higher than traditional PCBs. In addition, HDI boards have better improvements in radio frequency interference, electromagnetic wave interference, electrostatic discharge, and heat conduction.
Electronic products continue to develop toward high density and high precision. The so-called “high”, in addition to improving the performance of the machine, also reduces the size of the machine. High-density integration (HDI) technology can make terminal product designs more compact, while meeting higher standards of electronic performance and efficiency. At present, most popular electronic products, such as mobile phones, digital (camcorder) cameras, notebook computers, automotive electronics, etc., use HDI boards. With the upgrading of electronic products and market demand, the development of HDI boards will be very rapid.
Ordinary PCB introduction
PCB, called printed circuit board, is an important electronic component, a support for electronic components, and a carrier for electrical connection of electronic components. Because it is made by electronic printing, it is called a “printed” circuit board.
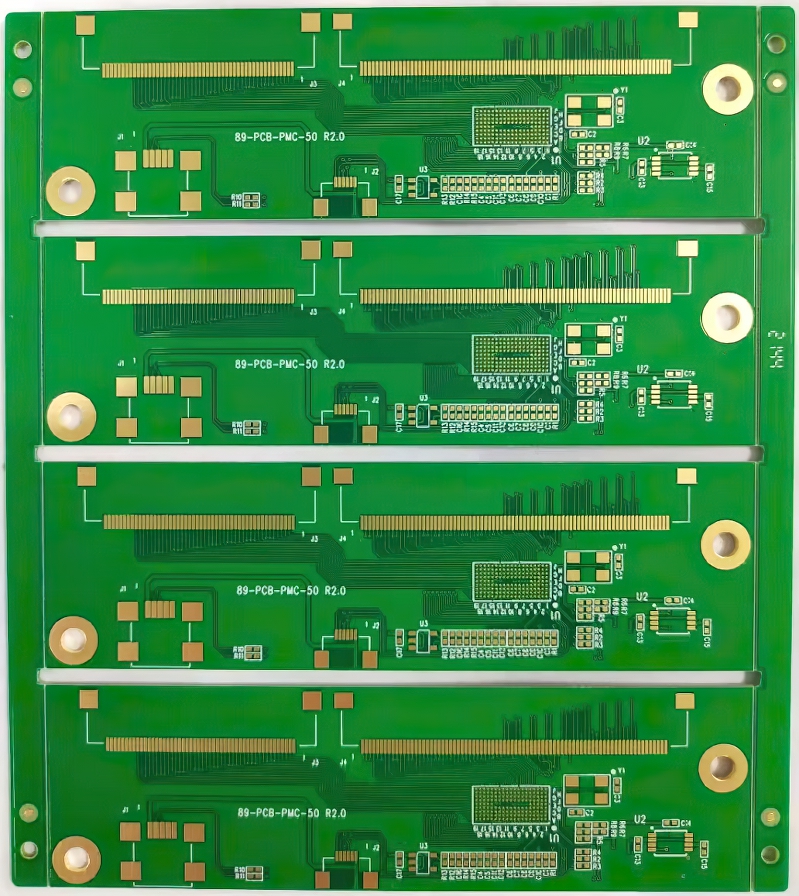
Its main function is that after electronic equipment adopts printed boards, due to the consistency of similar printed boards, manual wiring errors can be avoided, and electronic components can be automatically inserted or mounted, automatic soldering, automatic detection, and guarantee Improve the quality of electronic equipment, improve labor productivity, reduce costs, and facilitate maintenance.
Are PCB boards with blind and buried holes called hdi boards?
HDI boards are high-density interconnected circuit boards. The blind hole plating and second-time pressing are all HDI boards, which are divided into first-order, second-order, third-order, fourth-order, and fifth-order HDI. For example, the motherboard of iPhone 6 is fifth-order HDI.
Simply buried vias are not necessarily HDI.
How to distinguish HDI PCB first-order, second-order and third-order
The first-order is relatively simple, and the process and craftsmanship are well controlled.
The second order started to be troublesome, one was the alignment problem, and the other was the hole punching and copper plating problem. There are many types of second-order designs. One is that the positions of each step are staggered. When connecting the next adjacent layer, it is connected through a wire in the middle layer, which is equivalent to two first-order HDIs.
The second is that two first-order holes are overlapped, and the second-order is realized by superimposing. The processing is similar to two first-order holes, but there are many process points to be specially controlled, which is mentioned above.
The third is to punch directly from the outer layer to the third layer (or N-2 layer). The process is different from the previous one, and the difficulty of punching is also greater.
For the third-order analogy, it is the second-order analogy.
The difference between HDI board and ordinary PCB
Ordinary PCB board is mainly FR-4, which is laminated with epoxy resin and electronic grade glass cloth. Generally, traditional HDI uses backed copper foil on the outer surface. Because laser drilling cannot penetrate the glass cloth, glass fiber-free backed copper foil is generally used. However, the current high-energy laser drilling machine can penetrate 1180 glass cloth. There is no difference in this way from ordinary materials.
If you have any PCB demands, please feel free to contact us.
Email:[email protected]
Skype:[email protected]
Telephone number:+86 133 9241 2348
Whatsapp: +86 133 9241 2348