What is FPC flexible board ink?
FPC is a flexible circuit board, and FPC flexible board ink is an ink with bending resistance. In the past, FPC was produced with cover film, that is, dry film. Now many flexible circuit boards are produced with photosensitive ink or thermosetting ink, so circuit board ink is also called wet film.
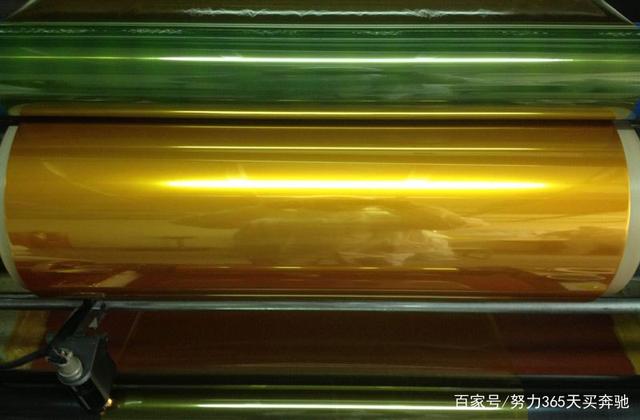
Solder mask inks are mostly green inks, so they are called green oil bridges, also called solder mask bridges and solder mask dams. Solder mask ink is an “isolation tape” made to prevent the short circuit of SMD component pins in the factory’s batch SMD production. In order to control the green oil bridge of the FPC soft board, it needs to be controlled during the solder mask process.
What is the role of FPC solder mask ink?
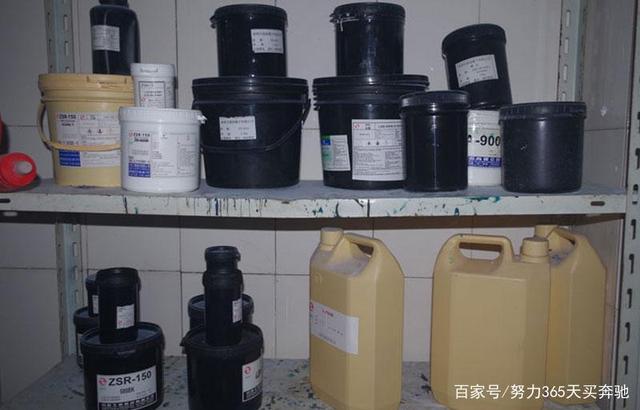
FPC solder mask ink is used in place of the original cover film, and its function is the same as that of the cover film.
Mainly play the following roles:
- The FPC flexible board ink is printed on the copper foil circuit on the surface of the circuit board, which isolates the copper foil from contact with the outside world and plays a role in surface insulation.
- After the circuit board is produced, it has to go through multiple processes. In order to prevent the copper foil circuit from being damaged during transportation and production, a protective layer should also be printed to protect the circuit and prevent circuit scars.
- After the circuit board solder mask ink is completely cured, it can well prevent conductive foreign objects from falling into the circuit and causing a short circuit.
- FPC circuit board solder resist ink has the functions of anti-electroplating, chemical tin resistance and chemical gold resistance, and can also play a good role in solder resist in SMT.
Therefore, in general, FPC soft board solder mask ink is a layer of protective paint, which plays a protective role to a large extent.
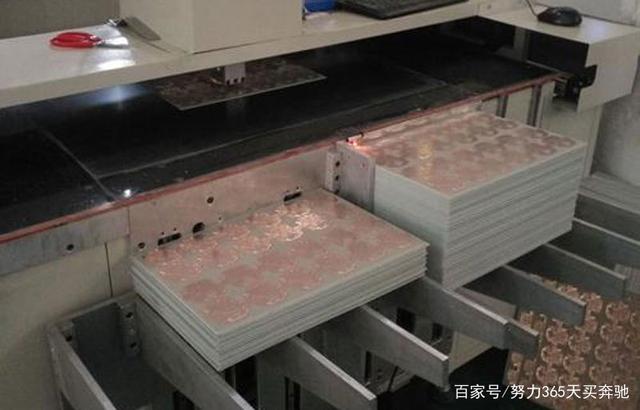
The ink used for solder mask is generally photosensitive, called liquid photosensitive ink. There are also a lot of solder resist inks that are thermally cured and baked, such as solder resist inks used on mobile phone antenna boards and character inks printed on circuit boards. There are also some UV light-curable inks, mainly green inks.
The ink on the circuit board generally has green, black, white, red, yellow, blue and so on. The cover film, generally yellow, black and white. Compared with the cover film, the color of the ink can be more diverse to meet the color requirements of various circuit board manufacturers. Black has good shading, white has high reflectivity, and white ink is more common in LED backlight soft boards.
What is the difference between overlay and solder mask inks?
The function of cover film and circuit board ink is the same, mainly because there will be some small differences in the production process. Now some precision circuit board production will still use cover film, but compared with cover film, the cost of silk screen printing ink It will be much lower, so most circuit board manufacturers will choose to use ink instead of cover film. With the development and improvement of inks over the years, many inks have fully possessed the same precision and bending resistance and resistance as cover films.
If you have any PCB demands, please feel free to contact us.
Email:[email protected]
Skype:[email protected]
Telephone number:+86 133 9241 2348
Whatsapp: +86 133 9241 2348